How IoT Is Going To Change The Manufacturing Process
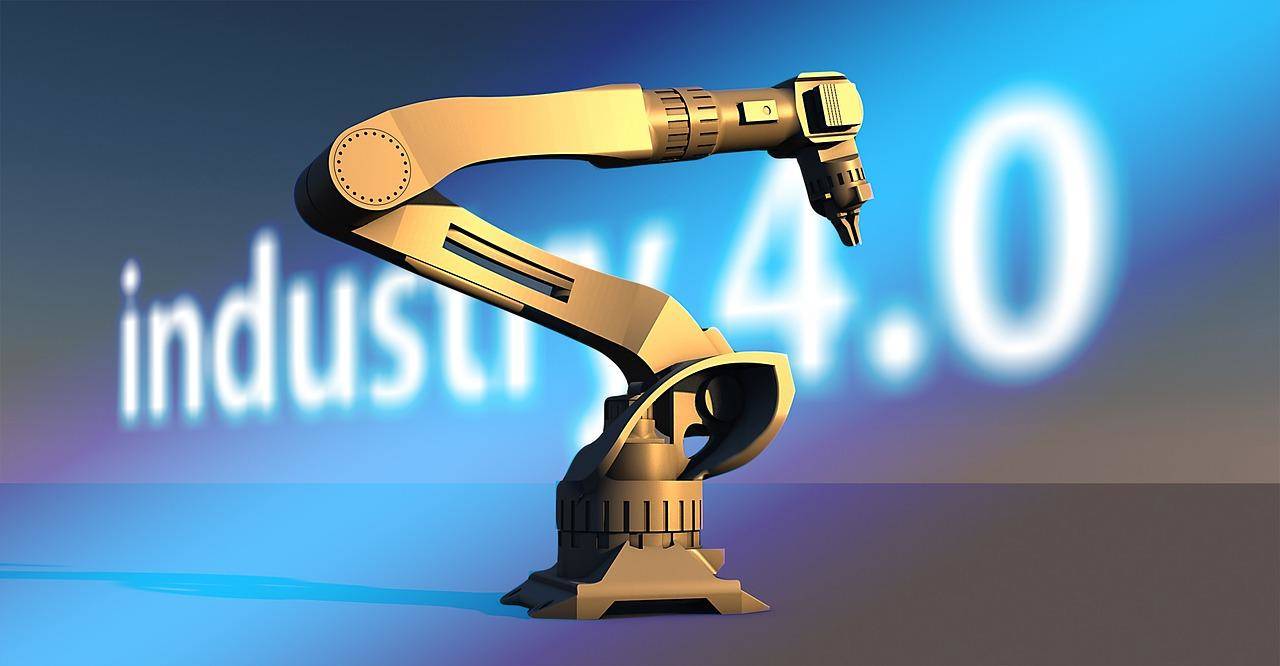
It is no secret that the world is going digital. Smart connected systems are becoming increasingly popular, as Internet of Things is changing logistics, travel, homes, business, and more. Thus, there is no reason why the manufacturing industry won’t be affected either.
McKinsey, one of the leading management consulting firms of the world, released an insight report on the economic impact of IoT applications. It suggests that by 2025 the impact will lie between US$ 3.9 trillion to $11.1 trillion, out of which about $1.2 trillion to $3.7 trillion will be reserved for IoT applications pertaining to the manufacturing industry. There will be a rise of smart manufacturing, which will be governed by an IoT ecosystem.
The future of manufacturing will be non-centralized, as factory objects will be a part of interconnected networks, and there won’t be any conventional hierarchy which we observe today. These objects will be able to self-organize, and field machines will prevail. Since consumer demands are increasing significantly, product processing itself will have to become so flexible that any object can be produced at minimum costs and times.
The signs are obvious. Today, customers can design their own products from their computer with a few clicks (customizable accessories, food products, etc.) and have them delivered to their homes within days, and even hours in some cases. Amazon’s drone system is already taking logistics and delivery to the next level, and setting an example which other retail giants are sure to follow.
The Pace of Change
Although there is a huge potential in an IoT based manufacturing industry, the changes won’t take overnight. We still have a long way to go, mainly because the existing system is quite robust and doesn’t give a reason strong enough for the manufacturers to adapt. At least not yet. There are many unanswered questions that are coming in the way of the revolution.
Factory planners and technology providers have to find concrete solutions to four major problems before IoT can penetrate the manufacturing industry on a large scale:
- How the manufacturing systems can exchange information through IoT network
- How to maintain control when hundreds of devices are operating simultaneously through a network that has even a larger number of connection points.
- How to establish a strong security protocol that can keep competitors and hackers at bay
- How to accurately predict the ROI on the investments in the IoT technologies
Of course, the best way to implement smart manufacturing is to start with a pilot project first. This will ensure minimum risks, and also help in learning what works and what not. This is the reason why most large enterprises working in the IoT technology have built their own smart manufacturing labs to test their technologies and devices.
A viable Solution
An excellent solution for the IoT based manufacturing centres to grow and become a standard soon, is to create an association in which commercial manufacturers and research companies work hand in hand. It can be a vast network that is comprised of both large and small corporations, all of which work towards a common goal. This setup can allow these companies to improve the factory technology with IoT in a realistic and pragmatic environment.
Another major advantage of the collaborative model is that it can help in the development of standards and regulations, which are quite essential for smart manufacturing to become a reality. Businesses that are a part of this collaboration can also benefit each other, by offering insights they possess. Research partners will also give an impetus to the application by observing its working from a different perspective.
An actual collaboration model has already been created by SmartFactoryKL. Their implementation of a highly advanced production line, which is based on Industrie 4.0 standards can easily be considered the perfect example of multi-vendor collaboration. If anything, a lot can be learnt from the model during the development of a pilot program.
The Developments
IIoT, or the Industrial Internet of Things wave is already changing the way factories operate today. While the IIoT revolution was mainly led by some of the biggest industrial tech giants such as IBM, General Electric, CIsco, etc. lately many startups are also emerging on the scene with their own grand implementation of the IoT technology:
- Extraction and Heavy Industry: Companies like Aptomar and Groundsensing are using sensor platforms that can be used in dangerous environments such as mining and construction. While the former is using IoT for spill safety, the latter is using it for locating oil wells. Another company called Skycatch is using drones for gathering data that can be used for developing 3D models of the construction sites.
- Supply Chain and Manufacturing Industry: There are many companies that are using IoT devices to gather data, which is used for enhancing the supply chain performance. For examples, CargoSense is using black boxes for detecting the movement of the containers as they are shipped. Similarly, there is a growing popularity of robots such as RoboCV that are specifically used in warehouses.
- Utilities and Smart Grid: Companies such as Bluepillar and Trilliant are using IoT for improving the efficiency of electricity, water, and gas distribution. They are providing radical solutions to large utility companies through smart-meters that provide data for usage monitoring and reporting.
Smart manufacturing is showing a lot of potential, and the existing efforts certainly support the belief. However, there are many problems that are yet to be overcome. The biggest of these is system interoperability. Incorporating minor elements of IoT in manufacturing is one thing, but building a full-fledged smart factory is a different ball game altogether.
Another major problem is to make a large number of companies to collaborate and push the technology further. However, it is a big step for the manufacturing industry, and it is going to take a while, but smart manufacturing is to come, and there are no two ways about it.